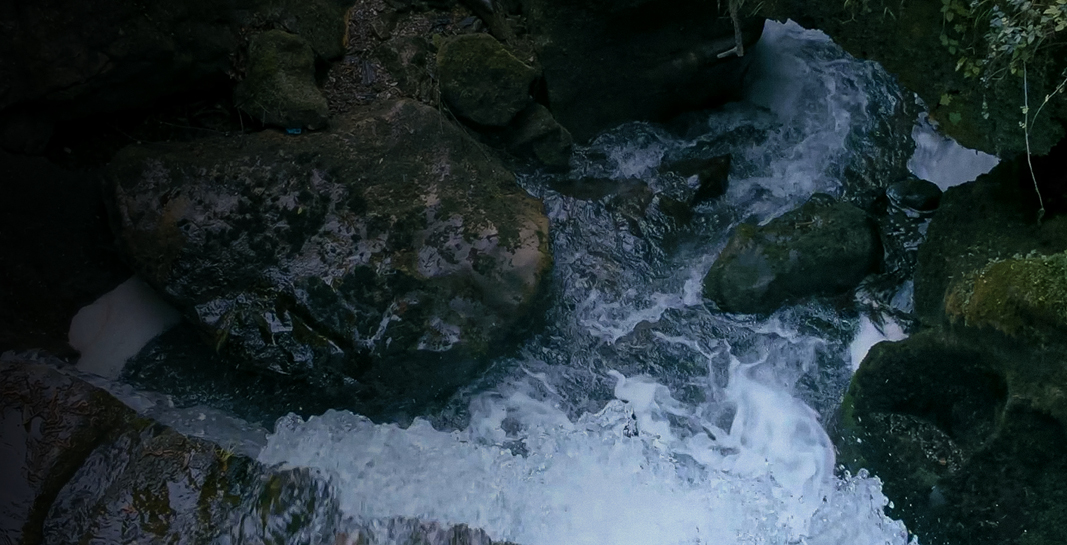
Safety and the 5S method
The 5S is a method to arrange spaces for every job to be done effectively, safely and efficiently. This system focuses on keeping everything in its intended slot and the workplace tidy, minimizing wasted time and the risk of personal injuries. 5S came about as the cornerstone of the Toyota Production System (TPS), the production method pioneered by the leaders of the Toyota Motor Company in the early to mid-20th century. This system, often referred to as Lean Manufacturing, aims at increasing the value of products and services for customers.
Far more than just an organizational approach, the 5S method is above all a shared management system to empower people with a view to improving organization, quality and safety at work, enhancing satisfaction and productivity.
What are 5S?
The term 5S stems from five Japanese words:
Seiri / Sort
The first pillar focuses on eliminating from the workplace items not needed for current production operations and deciding on an appropriate location for the items/tools needed instead. The sound implementation of this approach results in the reduction of problems and hindrances in the workflow.
Seiton / Set in order
The second passage involves arranging and organising items/tools in such a way to make them easy to identify, use and store. This leads to increased consistency and straight-linearity in production activities while reducing wasted time in manufacturing activities. Visual standards are used to evaluate the compliance and improvement of the second 5S point.
Seiso / Shine
The third task is to check the Tidiness and Cleanliness created. This activity requires that everything is tidy and clean, so that any items/tools are always available and ready for use.
Seiketsu / Standardize
The fourth passage, Standardize, is the method to maintain the first three pillars, ensuring them to be upheld and improved over time. Maintaining this philosophy is the only way to truly and effectively implement the fourth step.
Shitsuke / Sustain
The fifth step, Keeping in Time, aims to ensure the procedures put in place become a habit and are maintained, with improvements being made over time.
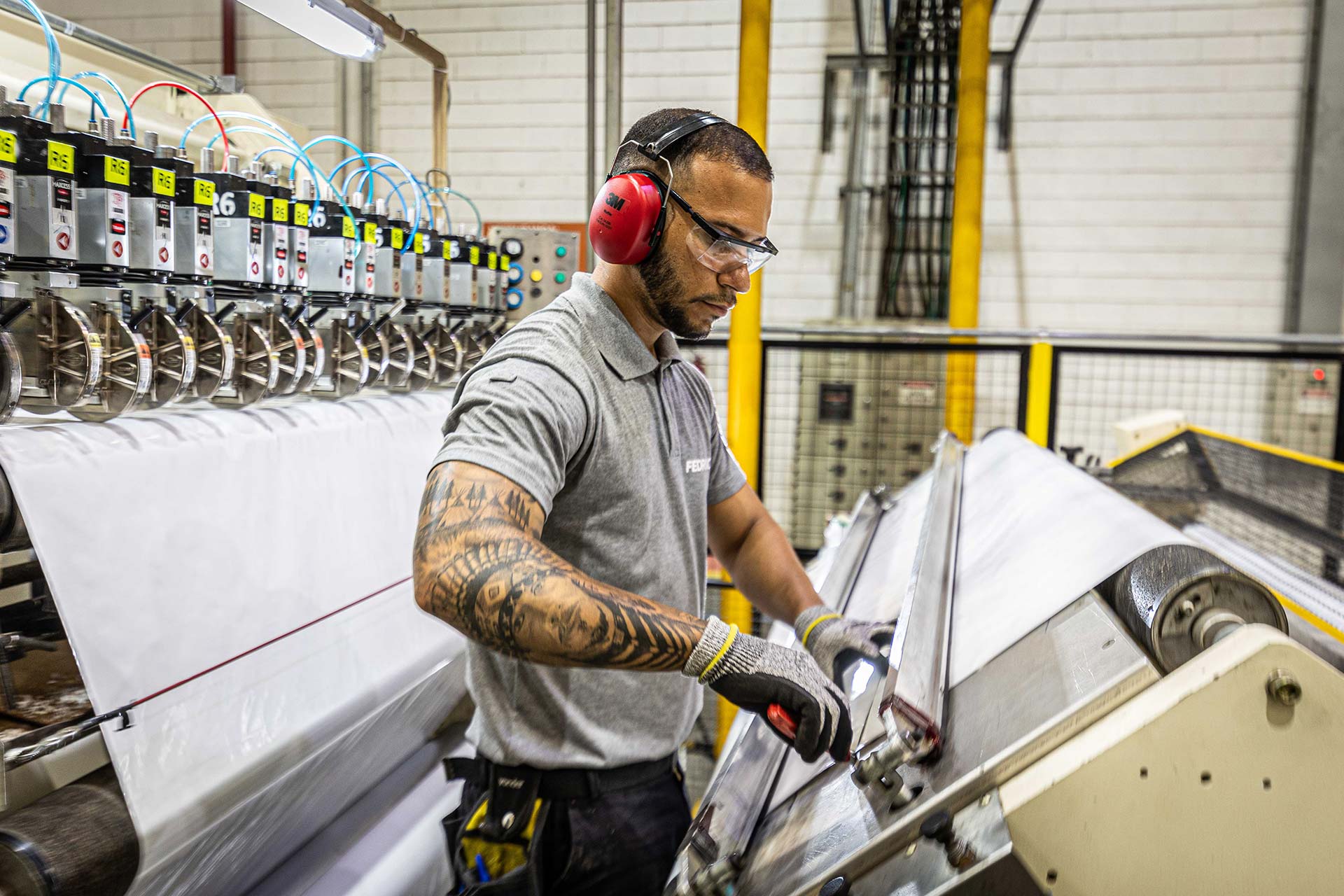