From waste to resource
Our commitment to the circular economy focuses on ensuring that our products, once they reach the end of their life, can either be reused or disposed of responsibly. To achieve this, we have set two ambitious 2030 targets. First, 100% of our products will be designed for optimal end-of-life recycling and recovery, with Life Cycle Assessments (LCA) available upon request (with a baseline set in 2022). Second, we aim to send 100% of our waste for recovery rather than for landfill disposal.
The choice of raw materials for our products is crucial, as it impacts not only the environment—such as through deforestation—but also society, particularly in terms of human rights. During the production phase, the impact is closely tied to the waste generated and how it is managed. At the end of our products’ life cycle, the potential for positive impact arises from recovering and reusing raw materials. To mitigate impacts on the environment, we adhere to the “waste hierarchy.” Our approach starts with preventing and reducing waste generation. When waste is unavoidable, we prioritize recycling and recovery.
The impact
By 2024, we achieved a 92% recovery rate for our waste, up from 90.0% in 2023, through a series of initiatives. These efforts included reducing packaging, recovering washing water, and implementing the circularity of sludge from paper mills, which is now used in other industrial sectors such as agriculture and bio-building materials. Additionally, we focused on recovering solvents from washing water and launched circularity initiatives, offering customers a waste collection service for self-adhesive materials with third-party support through RePlay. Furthermore, we began exploring solutions for managing the matrix (semi-finished waste), which is currently unused waste in the Self-Adhesives business unit.
The impact of the Self-Adhesive division
At the Self-Adhesives Business Unit, waste is the most important environmental aspect. The main waste is raw materials and semi-finished products (mixed waste) and the washing-water used to clean coating heads (both with water and solvents). All waste is collected, separated and, increasingly, sent for energy or material recovery.
Find out more about the Self-Adhesive commitment
The impact of the Special Papers division
The main waste in the Special Papers division is the sludge from the processing water, which, before being returned to the environment, is purified by primary chemical-physical plants and secondary biological plants. In addition to this waste, there is also mixed packaging, wood, plastic, production waste containing silicone, solutions/dispersions/emulsions of substances from machine washing, used oil, iron and electrical equipment, of which, hazardous material represents a very small proportion of our total production, below 5%.
Find out more about the Special Papers commitment
Our 2024 achievements
With these actions we directly contribute to the achievement of the Sustainable Development Goals (SDGs) 8 and 15.
92%
of industrial waste recovered
92%
of the Special Papers sites are ISO 14001 certified.
75%
of the Self-Adhesives production sites are ISO 14001 certified.
0
no cases of violations of waste management regulations in our production sites
Target:
100% of industrial waste recovered and not sent destined for landfills
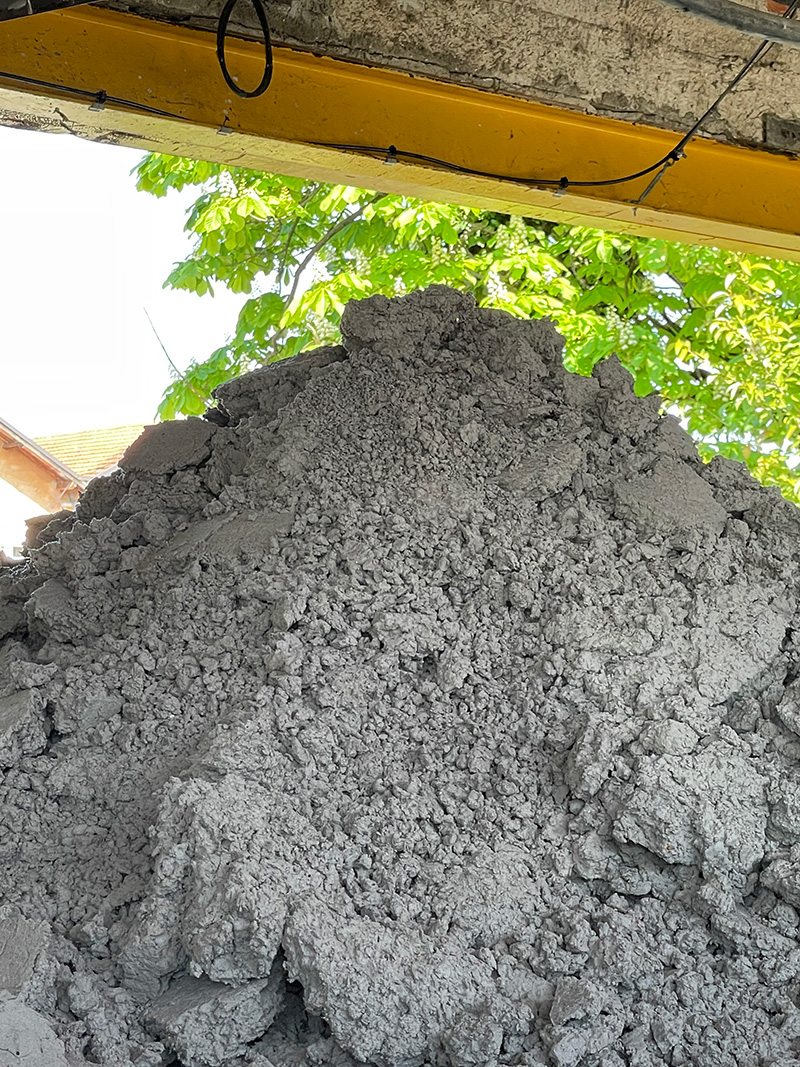
Sludge recycling and drying
We have installed a pilot drying plant in Verona, which enables us to reduce the volume of sludge produced, which was also done in Fabriano and Arco in 2021. The sludge can then be used by other production areas, such as the agriculture and bio-construction sectors.
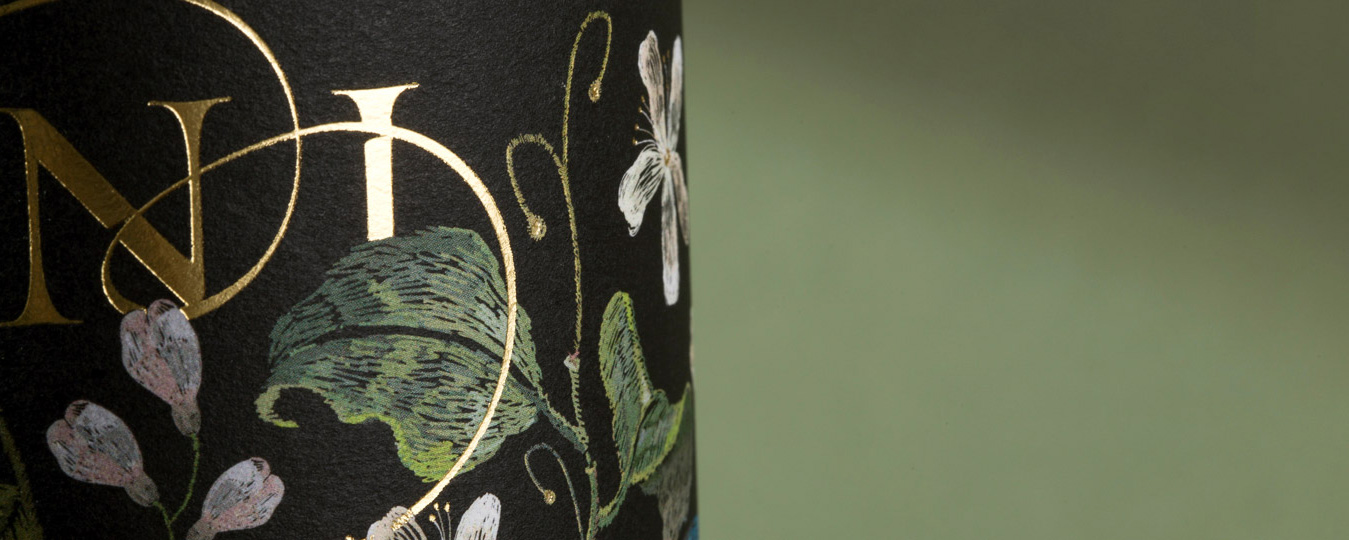
Differentiating, sorting and reusing
The first step is to precisely map the waste in each plant so that we know where each kilo of waste is produced so that it can be recovered or recycled. For example, all production waste is recycled in-house as fibrous raw material.