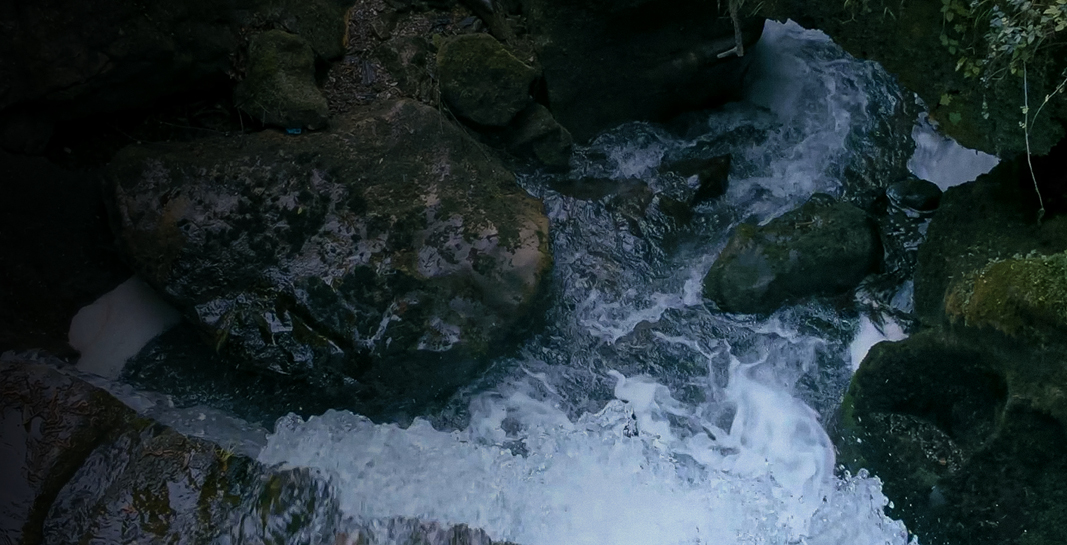
Self-adhesive material: what it is and how it is made
The label on a bottle of wine, the seal on a box of chocolates, the sticker on an apple, the graphic on a store window, the lettering on a public transit floor, the billboard by the side of the road, an inscription personalizing a commercial vehicle, the pharmaceutical sticker in the box of a medicine, a sticker card on the album, and more. Self-adhesive material is in our daily lives more than we can imagine: changing the appearance of objects, providing valuable information, tracking products, identifying spaces. The self-adhesive industry is much more technical and demanding than it sounds: in just a few millimeters is a bundle of innovation, chemistry, physics, and different materials.
A quality self-adhesive must meet the specific requirements of each customer, addressing needs for durability, safety, design, aesthetics, functionality and creativity. It must ensure the same performance over challenging conditions: temperature swings, extreme heat and cold, humidity, contact with water, oil and other potentially damaging substances
The key question first: what a self-adhesive material is and how it is made
Many insiders term it a “sandwich”: actually, its layered makeup may be somewhat resembling the iconic loaf of bread. It consists of three main components: front face, adhesive, and release liner.
- The facestock is the “visible” part, which is then printed, and can be made of paper or plastic film (PP, PE, PET, PVC)
- The adhesive is what makes the facestock stick to a surface and should be chosen bearing in mind the application surface material, the temperature the label will be applied at, and the required life span
- The release liner is the backing of the self-adhesive material and can be made of silicone-coated PET or paper. An additional layer of material (silicone) is between it and the actual adhesive, which allows the liner to be removed without dragging adhesive behind it.
The centerpiece of the material is precisely the adhesive with viscoelastic properties ‘activated’ by the pressure during application: this is why it is also referred to as pressure sensitive adhesive (PSA). It represents a key component for the customization and performance of final products, thanks to the use of different technologies offering the best solution for any need.
The facestock can be made of paper or plastic film; on many occasions the latter is the only material that can be used to ensure the function and life of the facestock, i.e., the excellent quality of the required product.
The release liner is the part of the self-adhesive material that is being extensively focused on to reduce its waste since, once removed, it turns to be discarded. Our latest solutions are born to solve this resource waste from the source by eliminating and/or recovering the production of process waste, turning the liner from waste into a new resource.
Fedrigoni Group pursues sustainability goals using paper when possible and plastic if necessary. The Self-Adhesives and Paper business units, keep working in synergy to achieve by 2030 the goal of offering 100% of products designed for optimal recycling and recovery at the end of life, with Life Cycle Assessment (LCA) on demand. Specifically, Fedrigoni Self-Adhesives aims to get 100% of standard product portfolio with a solution designed to be recyclable or reusable for packaging (recyclable, compostable, removable). A goal that can be achieved through the teamwork of our R&D teams.
Which industries do we serve?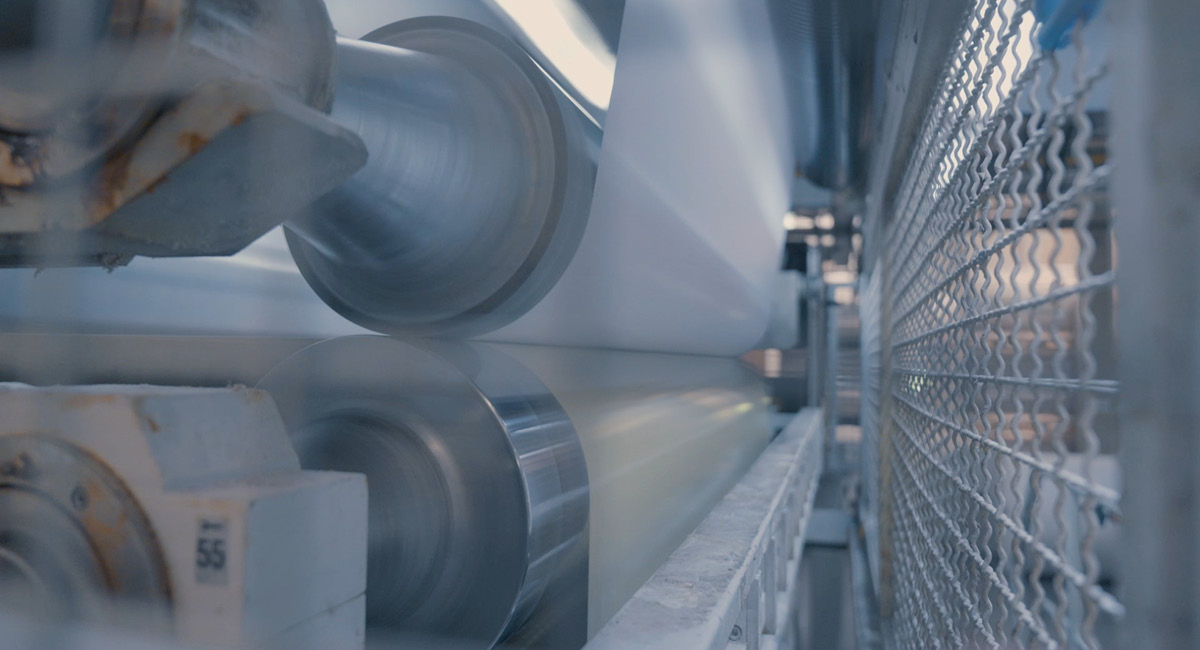