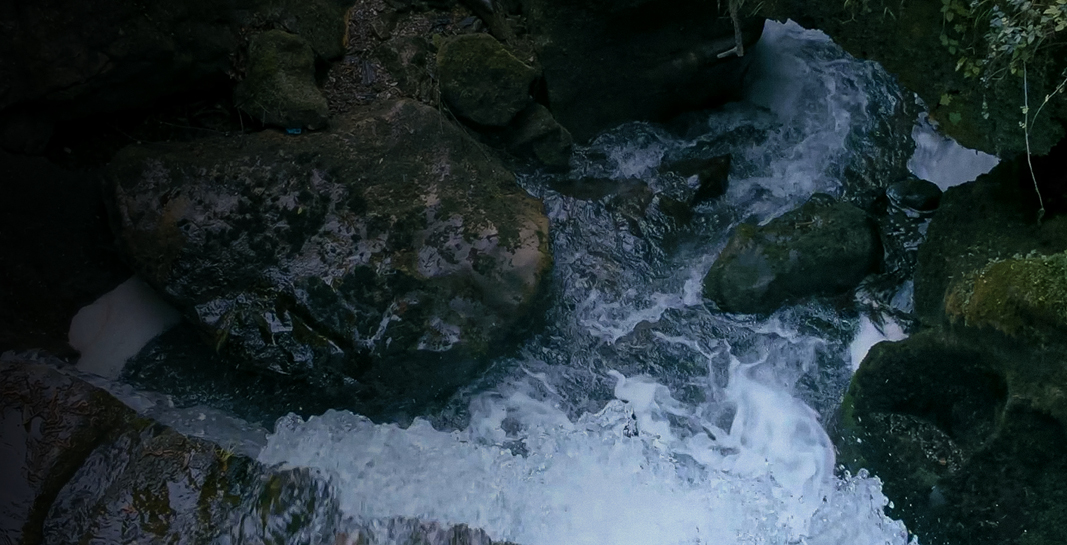
From fabric scraps to a new paper: the upcycling project with Albini_next
The term upcycling refers to a “recycling” process resulting in a more valuable end product compared to the basic scrap. As part of the circular economy, the result is a reduction in the waste of materials giving them a second life and optimizing the energy and emissions of each production process. High technical skills, creativity and innovation underpin this approach.
‘Futura – A revolutionary tradition’ is the upcycling project featured by ALBINI_next, a division of the Albini fabric group dedicated to sustainable innovation, with Fedrigoni’s R&D department. Micaela di Trana, VP Marketing and R&D at Fedrigoni Special Papers, tells us about it.
Futura is a great deal to me and to all the people engaged in this project from the very beginning. The story started off just at the beginning of my personal experience at Fedrigoni in February 2020, as one of the first many (almost impossible) projects I came across.
The Albini Group, already our customer and with a great drive for innovation, boasting the world’s first organic and traceable cotton, wondered how internal waste could be reused, upcycling-wise.
This same wondering led our collaboration and after two years of research and testing , a new paper made up of cellulose and fabric scraps from the cotton mill came to light. Crafting it out showed several challenges, mainly aiming to achieve high technical and aesthetic properties. We pulled out all our know-how in managing industrial paper processes, investing heavily in research and development and doing many tests.
In Fabriano mills in particular, we have been producing paper types consisting also of cotton fibers, usually pure, getting a softer paper, more like a fabric. The project with Albini, however, involved waste, mercerized cotton, very tricky to be processed with traditional industrial equipment. Moreover, the intended outcome was a stiff paper-fabric. How could we do that?
The making of FUTURA starts with the sorting of scraps, either from the weaving process or the sampling and quality control department, which are frayed and then dusted. Now, the cotton is added by Fedrigoni to the cellulose mixture to make a cardboard used to create the display stands for the Albini Group’s Denim collection and the Service Program of Albiate 1830 brand.
So far, about three tons of product with repeatable qualities and specific mechanical characteristics have been produced through this process, recovering 950 kg of fabric scraps. Thanks to this collaboration, we succeeded in making the impossible: turning the production waste obtained from the weaving process into a new raw material.
A pioneering project that made us grow and breakthrough, developing an innovative product: sheer determination, patience and passion make every challenge possible. Special thanks to our partners Cotonificio Albini & Albini_Next for working together sharing the same values.
To sum up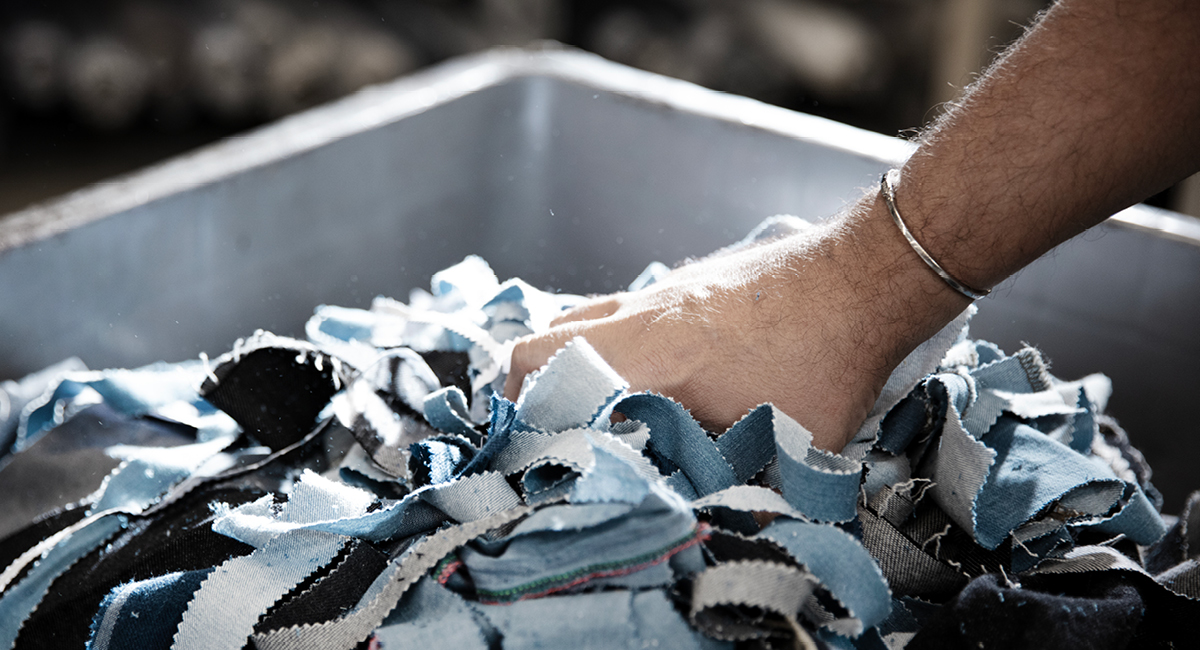