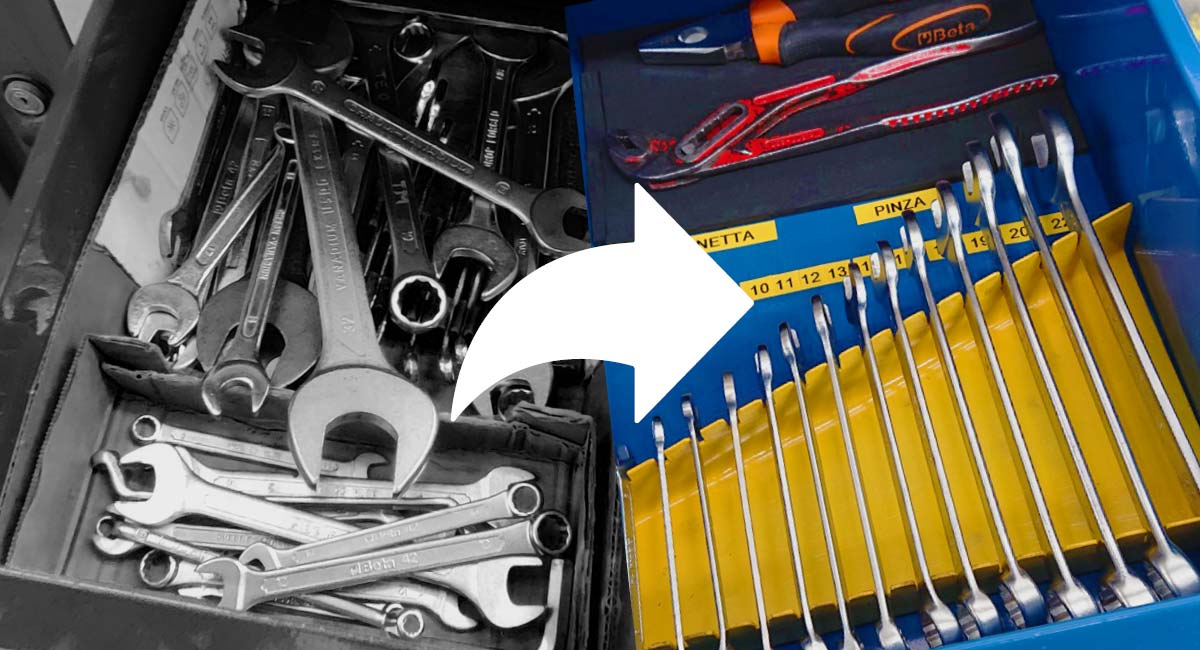
Approccio 5S: dal Giappone a Rocchetta, lo stabilimento situato nelle Marche sperimenta una nuova metodologia di lavoro
Seiri, Seiton, Seiso, Seiketsu, Shitsuke: queste 5 parole (che iniziano con 5 S) rappresentano i principi alla base di una metodologia che arriva dal Giappone, basata sull’eliminazione del superfluo e sull’ordine, pensata per ottimizzare l’organizzazione degli spazi di lavoro all’interno di stabilimenti manifatturieri, con il fine di mantenere un ambiente in cui si lavora in sicurezza e più efficacemente.
La metodologia 5S viene applicata da poco più di un anno anche nello stabilimento di Rocchetta, parte della cartiera di Fabriano (Gruppo Fedrigoni) che si occupa del taglio della carta, materiale che arriva qui in grandi bobine per essere trasformata in piccole risme A4 e A3 secondo le richieste dei clienti.
Mauro Chiucchi è stato il Responsabile stabilimento di Rocchetta fino al 30 marzo 2023 ed è la persona che ha promosso, con successo, l’utilizzo della metodologia 5S. Rocchetta ora rappresenta lo stabilimento ‘pilota’, con l’obiettivo di testarne l’applicabilità e in vista di una futura applicazione in altri siti produttivi del Gruppo.
“In stabilimento la nostra priorità è garantire condizioni di lavoro sicure e sane, con l’implementazione del metodo delle 5S cerchiamo di migliorare ulteriormente il nostro contesto lavorativo. Come? Agendo su due fronti: l’ambiente di lavoro e l’implementazione di nuove metodologie”, afferma Chiucchi.
“La prima sfida che ho incontrato è stata superare l’iniziale scetticismo da parte di alcuni collaboratori, i quali sostenevano che qui da noi questa metodologia non si potesse applicare. È normale che inizialmente ci siano punti di vista differenti quando si chiede di rivedere il modo di lavorare, ma pian piano, discutendone, siamo riusciti a convincere tutti che si potesse fare. Molti si sono appassionati e ad oggi sono tutti consapevoli dei miglioramenti ottenuti per il loro stesso benessere.”
Ma come funziona esattamente la metodologia delle 5S?
Lo spieghiamo facendo riferimento a come è stato realizzato a Rocchetta, stabilimento in cui vi sono degli impianti per il taglio di oltre 500 tonnellate di carta al giorno.
Prima di tutto c’è stato un momento di pianificazione che ha coinvolto un consulente esterno specializzato, un responsabile del progetto e altre figure interne che hanno seguito da vicino tutte le fasi per acquisire il know-how, diventando progressivamente esperti della metodologia. Attraverso diverse fasi, sono stati poi coinvolti nei gruppi di lavoro circa 80 persone, chiamate ad imparare le tecniche e a tradurre in pratica le attività stabilite.
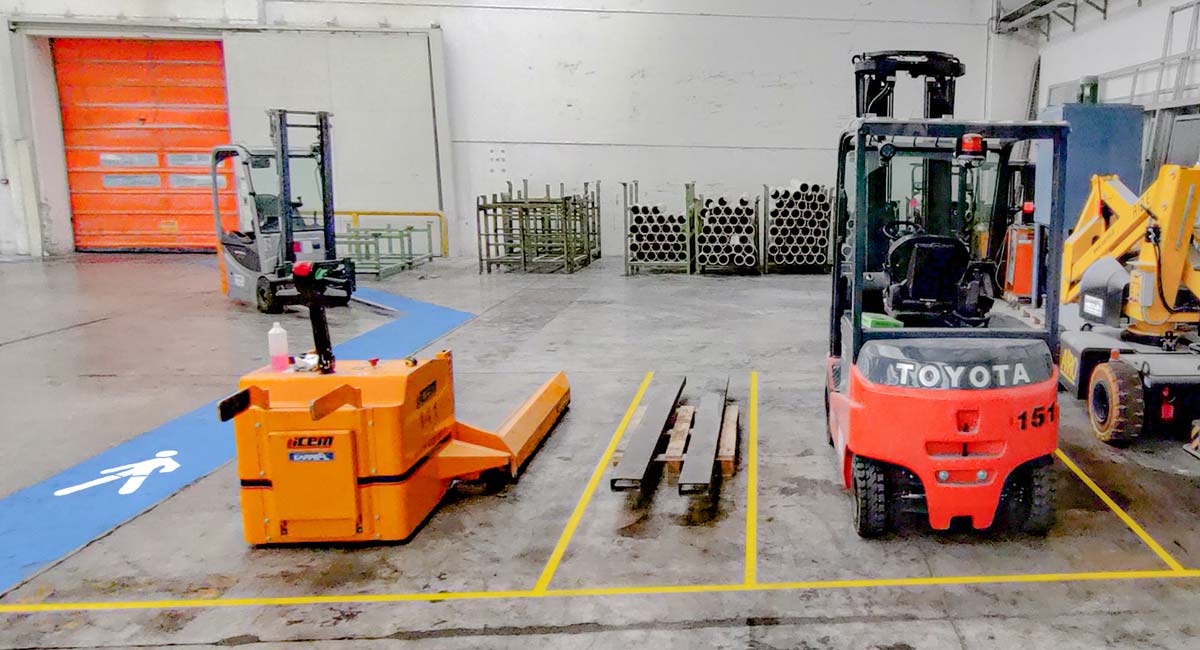
Definiti i team, si è suddivisa la superficie dello stabilimento per aree di intervento, sulle quali un po’ per volta si sono applicati i concetti 5S, seguendo queste tappe:
1 S (Seiri) separare il necessario dal superfluo, cioè si valuta nell’area oggetto d’intervento tutto il materiale che magari sta lì ma non serve, o serve solo momentaneamente o periodicamente, e lo si porta fuori, in una apposita area denominata “area rossa”;
2 S (Seiton) ordinare, “un posto per ogni cosa e ogni cosa al suo posto”, cioè si organizzano in modo intelligente i materiali che erano stati portati fuori, con un ordine che permetta di averli a portata di mano quando servono, riducendo il tempo di ricerca;
3 S (Seiso) pulire e ispezionare l’area di lavoro ed eseguire piccoli interventi sui macchinari, controllando che le attrezzature siano in ordine;
4 S (Seiketsu) standardizzare, sulla base di quanto si è fatto con le prime tre “S”, si stabiliscono delle regole su come e quando i compiti devono essere eseguiti. Questi standard possono comprendere programmi delle aree di pulizia e l’organizzazione degli spazi;
5 S (Shitsuke) mantenere, si devono fare verifiche periodiche per monitorare il livello raggiunto e realizzare i miglioramenti possibili.
“I punti più difficili sono proprio gli ultimi due, in particolare mantenere nel tempo, ma devo dire che ho riscontrato molta collaborazione, dal momento che ci si è resi subito conto dei vantaggi. L’ambiente di lavoro diventa più ordinato e pulito e quindi lavorare in uno spazio simile risulta più gradevole, appagante e meno stressante. C’è un vantaggio in termini di benessere, oltre a una maggiore sicurezza; si crea dello spazio libero eliminando il superfluo, i passaggi sono migliori e non ci sono materiali che intralciano, le persone lavorano meglio in postazione e hanno i loro attrezzi a portata di mano. Inoltre, questo approccio insegna a lavorare in gruppo e con metodicità”.
La realizzazione del progetto è stata divisa in due anni, un tempo ritenuto ottimale per far sì che le persone acquisiscano e facciano propria la metodologia, trasformandola nel normale modus operandi. “Realizzare questo progetto troppo velocemente può farlo fallire. È fondamentale che le persone si sentano coinvolte e responsabilizzate, con il rispetto dei tempi giusti, collaborando per un fine comune di cui tutti possono vedere direttamente il beneficio. Sono loro con il Team che, in definitiva, decidono gli interventi da fare per migliorare una certa area e gli spazi, non c’è nulla di ‘calato’, sono loro che prendono decisioni in merito e le possono sempre migliorare con nuovi suggerimenti, nel rispetto delle regole. I progetti 5S sono degli operatori che ci lavorano”.
Scopri di più sulla metodologia delle 5S in questa Pillola di Sostenibilità